Stockage
En 2021, le fabricant de cuves industrielles en thermoplastique Stockage & Systèmes avait fait l'acquisition du spécialiste belge des cuves extrudées enroulées EELIX SA (anciennement Technologie Schoeller Allibert). Depuis 2022, la technologie Schoeller Allibert a été relocalisée en France dans une usine située dans la Somme (80).
La technologie de cuves extrudées enroulées Schoeller Allibert dédiée au stockage de produits chimiques concentrés est reconnue depuis plus de 50 ans par les industriels, tous secteurs d'activités confondus. En 2016, elle était passée aux mains de la société franco-belge EELIX, qui avait repris tous les actifs de l'usine de production. Denis Megemont, dirigeant de Stockage & Systèmes, EELIX Belgique et EELIX France, témoigne : « Toutes les sociétés industrielles en France se sont équipées, tôt ou tard dans leur histoire, de cuves Schoeller Allibert, que ce soit dans le monde de la sidérurgie, de l'agroalimentaire, des boissons, du nucléaire, du traitement de l'eau, etc. EELIX SA (à l'époque détenu à 80 % par un groupe belge et 20% par Stockage & Systèmes) avait été sélectionné sans débat par Schoeller Allibert grâce à sa connaissance du marché et à sa capacité à redonner aux cuves fabriquées par extrusion-enroulement la position technique et commerciale dont le marché a besoin. La société ayant été considérée comme la seule capable d'assurer la continuité de cette technologie. » Après le rachat, l'outil de production avait été transféré en Belgique, dans une usine située en Wallonie, près de Liège. Pendant cinq années, EELIX a principalement rayonné sur la Belgique, les Pays-Bas et le Luxembourg, tout en continuant à servir le marché français.
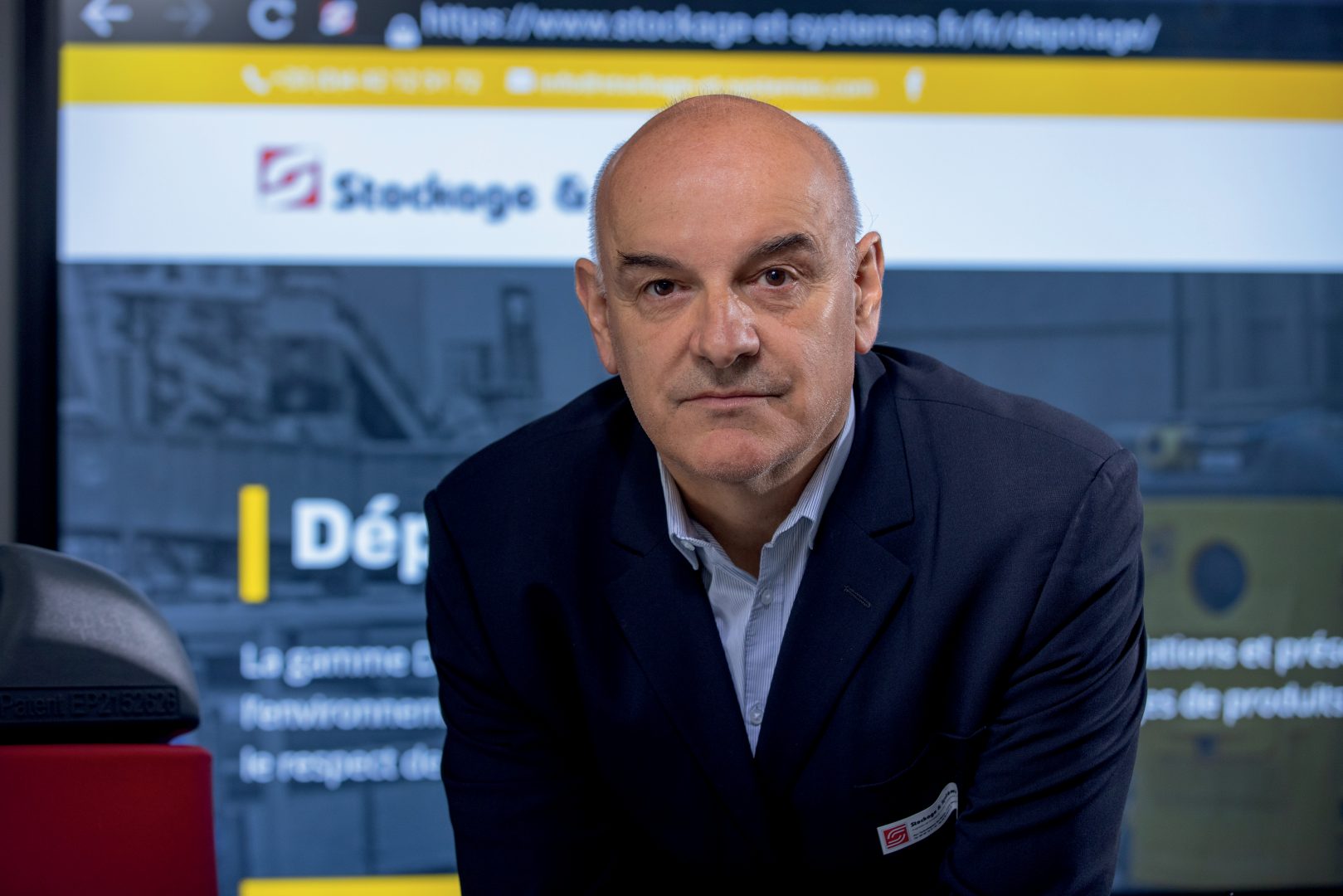
L’ancienne usine belge trop limitée
Les industriels ont besoin de solutions de stockage performantes pour des applications complexes, aussi bien à l'égard de la réglementation, que du produit à stocker ou du volume de stockage, et les cuves par extrusion-enroulement permettent, entre autres, de fabriquer des cuves de plus grands volumes en PEHD et PP ce que seule cette , technologie permet de façon industrielle et pérenne. Après le déménagement de l'outil de production en Belgique, EELIX s'est rendu compte que la technologie manquait au marché français. Le dirigeant explique que « la fabrication de cuves extrudées enroulées grands volumes nécessite de grands espaces de fabrication, si bien que nous étions limités par les dimensions de notre usine belge. Nous n'étions pas en mesure de répondre à toutes les demandes, les industriels nous ayant notamment challengé pour la fabrication de volumes de plus en plus grands. » Les dimensions de l'usine belge n'étaient plus suffisamment adaptées, que ce soit en termes de surface au sol, de hauteur de bâtiments, de puissance électrique ou de zone de stockage.
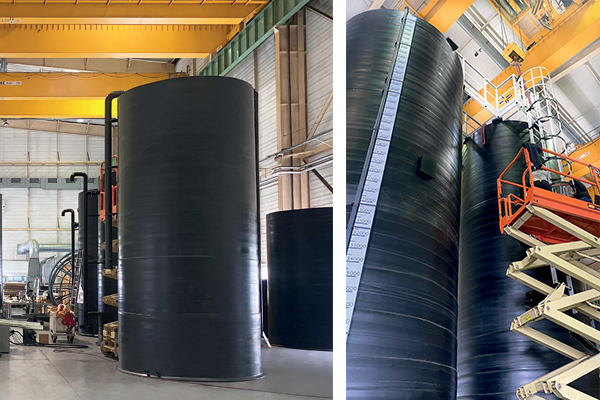
Stockage & Systèmes à Pollutec 2023
Stockage & Systèmes et EELIX seront exposants au salon Pollutec, qui se tiendra du 10 au 13 octobre 2023 à Eurexpo Lyon.
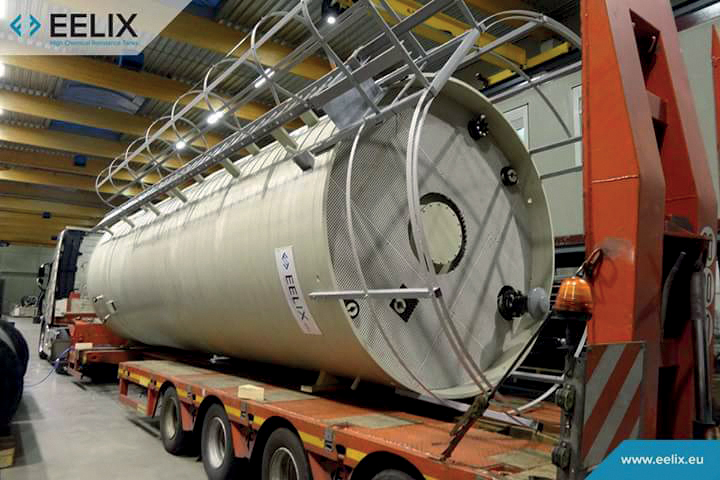
Implantation dans les Hauts-de-France
En 2021, la société Stockage & Systèmes a racheté la totalité des actifs d'EELIX Belgique et a rapidement cherché à faire évoluer l'outil de production, en s'installant notamment sur un nouveau site de fabrication plus adapté. « Nous avons d'abord cherché à nous installer en Belgique, dans la région wallonne, mais nous ne trouvions pas les bâtiments adaptés à notre activité, précise Denis Megemont. Nous avons élargi nos recherches sur un axe Beauvais-Liège avec pour objectif de rester au plus près de nos clients. » C'est finalement à Albert (80) que la nouvelle usine a été implantée. La région Hauts-de-France est relativement attractive pour les industriels étrangers puisqu'elle favorise leur implantation sur le territoire. « La position géographique de notre nouvelle usine est également avantageuse du fait de la proximité de tous les services dont nous avons besoin, que ce soit en termes d'utilités, de maintenance, de matériaux ou encore de sous-traitance. Nous profitons d'un réseau de partenaires situés dans un rayon de 15 km autour de l'usine, et l'usine est à guère plus de 15 minutes de l'axe Lille-Paris. » Le siège d'EELIX Belgique reste à Herstal, en Belgique, et la totalité de la fabrication est désormais réalisée en France.
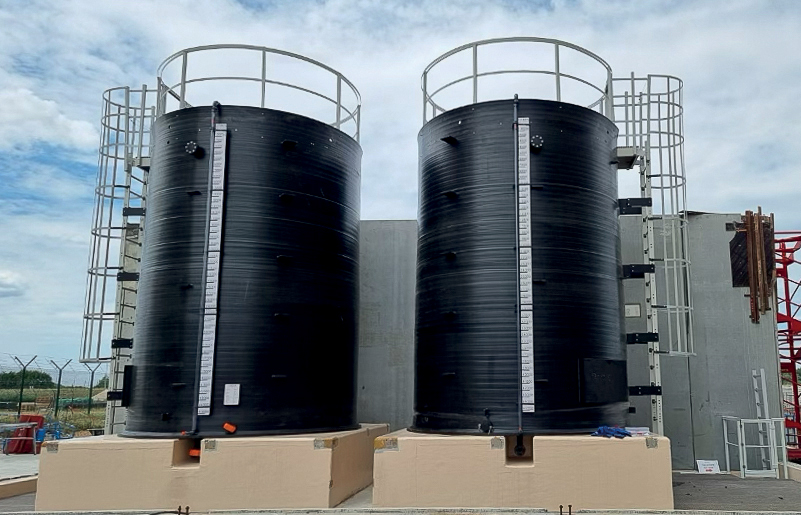
Un format hors normes
EELIX a trouvé l'infrastructure qu'il lui fallait pour poursuivre sereinement ses activités. L'usine d'Albert, qui offre plusieurs bâtiments pour 7 000 m², était notamment disponible avec l'alimentation en gaz et la puissance électrique nécessaires au process. Denis Megemont précise : « Nous disposons d'un hall principal de 2 500 m² de 15 mètres de haut et équipé de plusieurs ponts roulants de 60 tonnes, ainsi que d'une surface de stockage extérieure de 15 000 m². Les manutentions nécessaires dans notre métier pour les cuves en cours de fabrication et pour les mandrins d'enroulement sont réalisées sans contrainte d'espace, ce qui fluidifie le process. Notre nouvelle usine est une véritable cathédrale ! » L'usine est fonctionnelle depuis octobre 2022 et en pleine croissance. EELIX y a réalisé plusieurs investissements : le constructeur a notamment augmenté ses capacités grâce à de nouveaux mandrins (jusqu'à 3 500 mm de diamètre) pour la fabrication de cuves jusqu'à 70 000 litres et surtout des mandrins plus longs pour des cuves sans manchonnage. « Ces investissements apportent des avantages techniques considérables pour nos clients et des gains de temps importants dans la fabrication. C'est totalement inédit en Europe, précise Denis Megemont. Aujourd'hui, la technologie est parfaitement sous contrôle. » Parallèlement, des investissements ont été réalisées dans des systèmes de soudage automatiques et dans diverses machines d'automatisation. Autre nouveauté : l'usine est aussi capable de fabriquer des cuves en plaques cintrées. « Grâce à la surface et aux outils disponibles dans l'usine, nous avons créé une ligne de production de cuves en plaques cintrées, ajoute Denis Megemont. Cette technique nous permet de proposer des cuves de petits volumes, pour des produits moins à risque et à des coûts plus attractifs. »
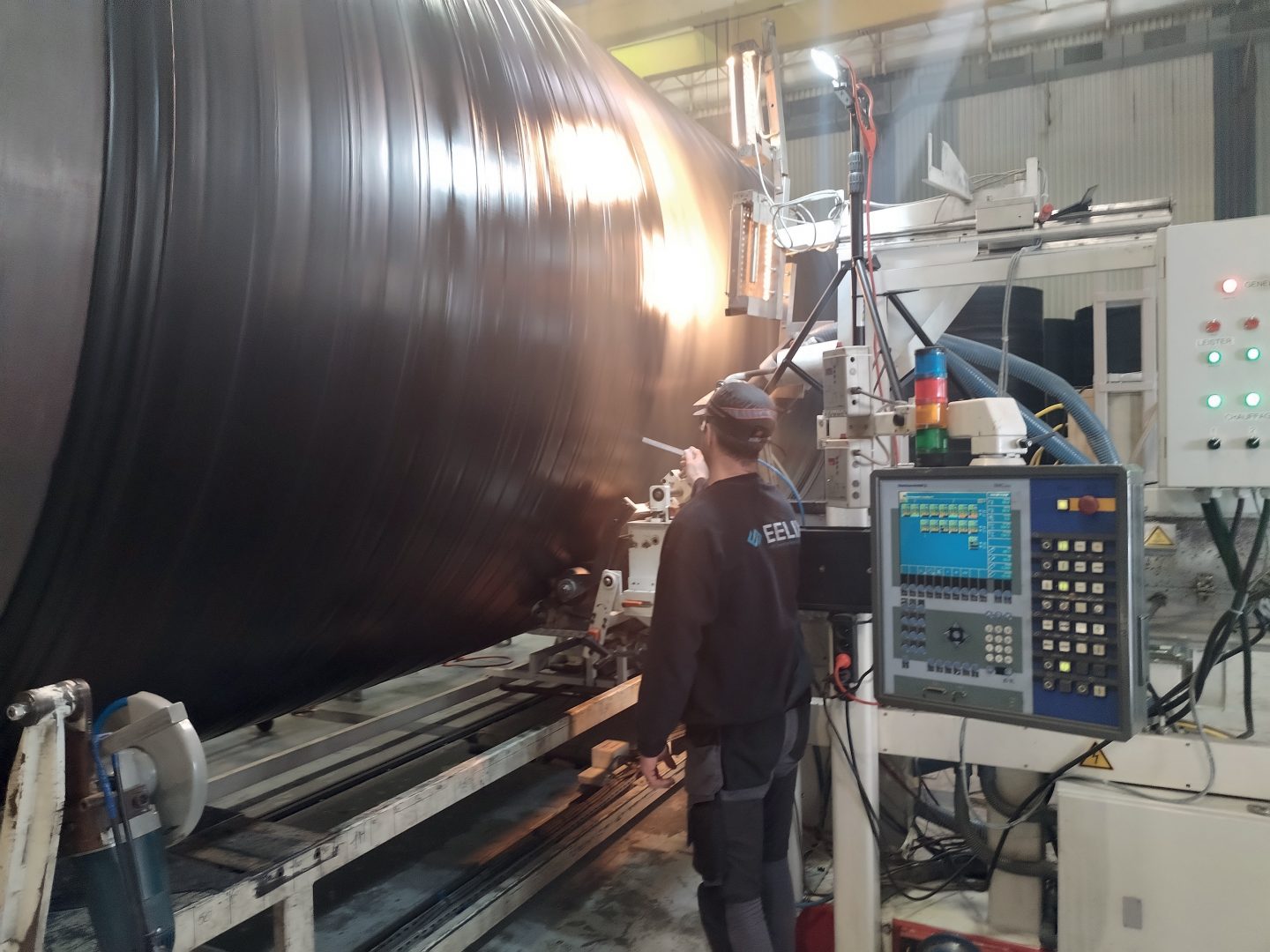
Le marché français en demande
Pendant 50 ans, Schoeller Allibert a vendu plus de 1 000 cuves par an à travers le monde. Depuis, elles sont largement reconnues par toute l'industrie pour leur qualité unique et leur longévité. « Il n'est d'ailleurs pas rare de rencontrer des cuves en service depuis plus de 30 ans », indique Denis Megemont. Après la relocalisation de l'outil de production en Belgique, les industriels français avaient pu ressentir un manque sur le marché et certains se sont tournés vers des constructeurs étrangers chez qui ils se fournissaient directement ou via des revendeurs. Cela n'était pas sans impact sur le coût du transport et sur la quasi-impossibilité de « tracer » la fabrication des cuves ainsi achetées. « L'unique détenteur de la technologie Schoeller Allibert est de retour en France, déclare Denis Megemont. Les industriels ont désormais de nouveau la solution ici en France et n'ont plus besoin de se conformer aux conditions d'importation et des intermédiaires. » Après avoir souffert de l'absence de la technologie, le marché français peut de nouveau en profiter. « L'usine est prête à répondre à tous les besoins. »
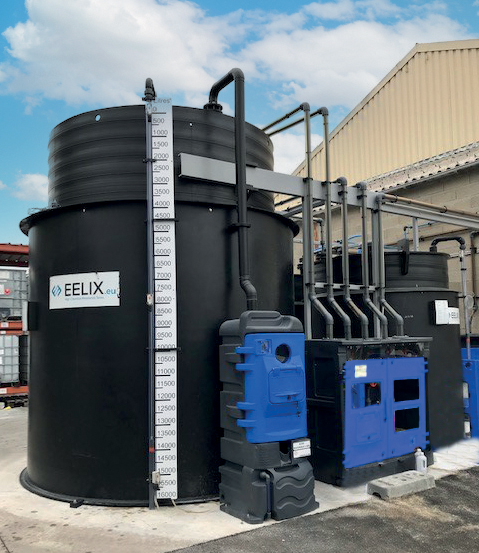
La technologie d’extrusion-enroulement
Depuis 50 ans, les cuves fabriquées selon la technologie de l'extrusion-enroulement Schoeller Allibert en polyéthylène haute densité (PEHD) et polypropylène (PPH) sont préférées à toutes les autres pour le stockage des liquides les plus corrosifs, lourds ou oxydants. En effet, grâce à leur technologie de fabrication, elles offrent une bien meilleure résistance. Les matériaux sont conformes aux normes alimentaires et 100 % recyclables. Elles sont d'autant plus utiles dans les cas de grands volumes (20, 30, 40, 50, jusqu'à 70 m3). Là où d'autres cuves seraient fabriquées par assemblage à froid et empilage de plaques, les cuves sont fabriquées par le procédé de l'extrusion-enroulement. Les granulés de matière première sont directement extrudés à haute température autour d'un mandrin (matrice) sous forme d'une « bande » qui s'enroule à sa température de fusion. Cette bande parfaitement homogène s'enroule naturellement à chaud pour devenir le corps principal (virole) de la future cuve de stockage. Selon la cuve à fabriquer (ses dimensions, la densité du liquide à stocker, les coefficients applicables, les conditions propres à l'installation à créer), la virole pourra atteindre de très grosses épaisseurs (25, 30, 40, jusqu'à 90 mm) sans aucune restriction technique. Cela avec une parfaite homogénéité et sans aucune contrainte mécanique.